The manufacturing industry has consistently used technology to fuel innovation, production optimization and operations. Now, with the combination of edge computing and AI/ML, manufacturers can benefit from bringing processing power closer to data that, when put into action faster, can help to proactively discover of potential errors at the assembly line, help improve product quality, and even reduce potential downtime through predictive maintenance and in the unlikely event of a drop in communications with a central/core site, individual manufacturing plants can continue to operate.
But this revolution of process and data requires many complex systems: sensors, line servers, wireless gateways, operational dashboards, servers and tablets for the maintenance teams on the floor to monitor the whole system. Unlike the factory systems of the past that were custom built and managed by operations technology (OT), the desired approach to support use cases that not only collect, analyze and act on machine, plant, and factory floor data in real time is to do so in a standardized manner.
To achieve this manufacturing vision, along with the continued digitalization of factories, manufacturers must now take a hard look at their operations and technology to meet these new opportunities. It requires factory systems to mirror the best practices of a modern IT environment based on containers, Kubernetes, agile development, AI/ML and automation. All of these technologies, coincidentally, are components of open hybrid cloud, an IT footprint that can be used to accommodate these manufacturing technologies, from the edge of the network to the factory floor.
What does it take? Let’s break it down
Let’s examine a manufacturing use case that needs to capture sensor information from line servers and route it to the on-site factory cluster where data can be analyzed in real-time with AI/ML models. This data can then be sent to the centralized data center or cloud for further processing and storage. We’ll cover how within this use case, what is done in a single plant/location, can scale to multiple sites with consistency to meet the needs of modern manufacturing organizations including:
-
A production model: manage the complexity and relationships of manufacturing “silos” and links in the supply chain.
-
Real-time processing and analysis of data: ability to monitor orders, materials, machine status, shipments.
-
Failure prediction (predictive maintenance): anticipate and act on production line events before they occur.
-
Security: conformance to corporate and government IT security policies.
-
Compliance: auditing of factory and core data center systems using operational and historical record keeping.
-
Modularity: transition from monolithic production systems to microservices.
-
Factory modernization: IT systems that can adapt to factory production line changes.
-
Safety: workers and equipment can be monitored continuously and many issues can be detected much earlier.
Meeting the needs of consistency and intelligence at the edge
In order to meet the needs of modern manufacturing organizations, it's important to acknowledge that manufacturing customers are under tremendous pressure to drive innovation and efficiency on their plant floors. This requires a holistic approach that incorporates a combination of modern IT products and emerging methodologies with the goal being to avoid the tedious and error-prone manual configuration of different systems and applications at scale.
Among the top considerations for building the edge architecture for this one manufacturing plant is that it needs to be scalable to hundreds of factories, without needing much manual intervention and increase in resources to manage them.
In addition, it needs sophisticated data messaging between potentially disconnected systems, robust storage for data from the factory line servers to the corporate data lake and integrated machine learning (ML) components and pipelines for delivering factory automation intelligence. Also, the hardware footprint for manufacturing systems can vary dramatically from low power, low memory units for data collection on the factory floor, all the way up to multi-core, large memory nodes in a central data center.
Two fundamental strategies that can help achieve this are:
-
GitOps and blueprints
-
AI/ML
GitOps and Blueprints
GitOps is a paradigm whereby enterprises use git as the declarative source of truth for the continuous deployment (CD) of system updates. Administrators can carefully and efficiently manage system complexity by pushing reviewed commit changes of configuration settings and artifacts to git, where they are then automatically pushed into operational systems. The idea is that the current state of complex distributed systems can be reflected within git as code.
In Kubernetes, GitOps is a powerful abstraction since it mirrors the underlying design goals of that platform: a Kubernetes cluster is always reconciling to a point of truth with respect to what developers and administrators have declared should be the target state of the cluster. An ideal GitOps model for Kubernetes employs a pipeline approach where YAML-based configuration and container image changes can originate as git commits that then trigger activities in the pipeline that result in updates to applications and indeed the cluster itself. Below is a graphical representation of a GitOps flow:
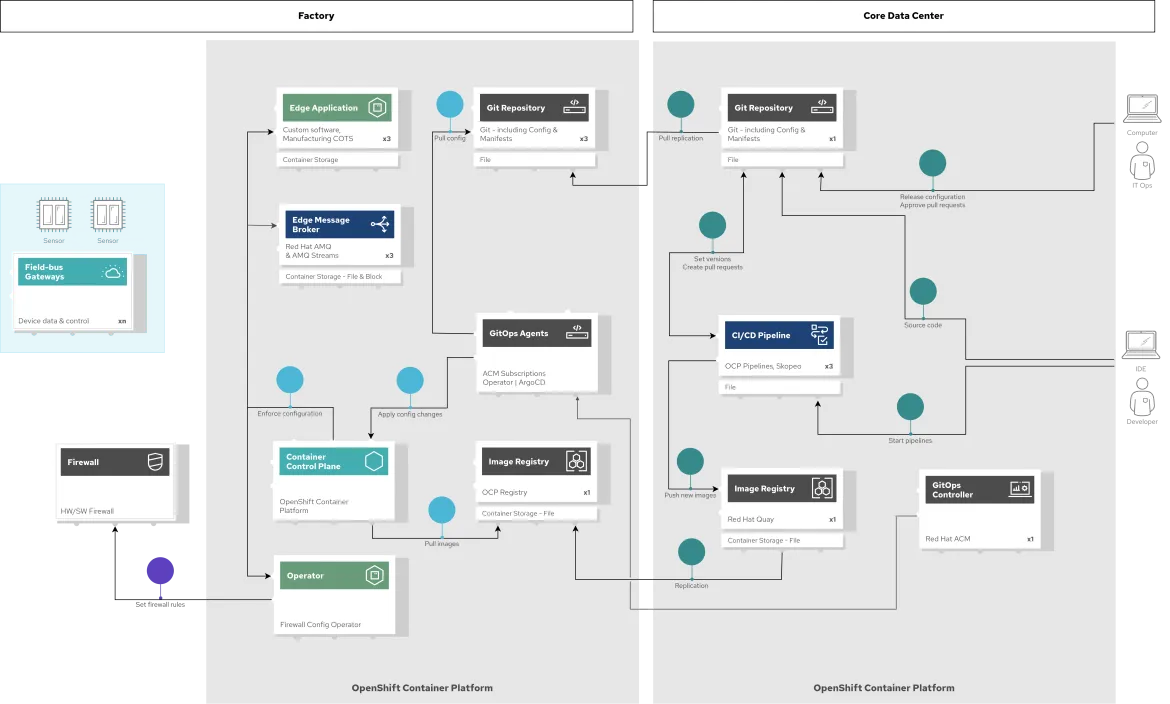
So for manufacturing environments, we can see the utility of something like GitOps for a consistent, declarative approach to managing individual cluster changes and upgrades. But we also know that edge manufacturing environments are heterogeneous in their size and type of hardware resources.
This is where the concept of blueprints comes in: declarative specifications that can be organized in layers such that infrastructure settings that can be shared are shared, but also allow for various points of customization where it is required. Blueprints are used to define all the components used within an edge reference architecture such as hardware, software, management tools, and point of delivery (PoD) tooling.
AI/ML to turn insights into action
Given that this use case involves the generation of large amounts of sensor data, we need to turn to AI/ML capabilities to produce actionable insights from that data. Human operators need to be able to view HMI/SCADA (Human Machine Interface/Supervisory control and data acquisition) dashboards in the factory of not only the real-time status of production lines, but also be presented with predictive information of factory health. The data from the line servers serves two purposes for AI/ML:
-
To drive the development, testing and deployment of machine learning models for predictive maintenance
-
To provide live data streams into those deployed models for inference at the factory
The below diagram depicts a sample AI/ML workflow:

Addressing industrial manufacturing use cases with Red Hat
Red Hat provides a technology advantage for manufacturers today with a portfolio of building blocks organized around Red Hat OpenShift, the industry’s most comprehensive enterprise Kubernetes platform. Red Hat products can be deployed and managed as scalable infrastructure for manufacturing use cases in an automated and repeatable way, and also coordinate the data messaging, storage, and machine learning (ML) pipeline.
Using a modular approach to building the edge architecture (see below) provides the flexibility to deploy any of the components shown where it makes sense — from the core data center to the factory floor, to address the needs of various manufacturing use cases.

What’s also important is having a reliable message queue that can hand off data to a scalable storage system as part of an open hybrid cloud model. Such a system manages the flow of data from the sensors all the way to the long term storage systems. Here is a breakdown of how the Red Hat portfolio works together to address the needs of our manufacturing use case:
-
OpenShift provides the robust, holistically secure and scalable enterprise container platform.
-
Data coming from sensors is transmitted over MQTT to Red Hat AMQ, which routes sensor data for two purposes: model development in the core data center and live inferencing in the factory data centers. The data is then relayed on to Red Hat AMQ Streams (Kafka) for further distribution within the factory datacenter and out to the core data center.
-
The lightweight Apache Camel K provides MQTT (Message Queuing Telemetry Transport) integration that normalizes and routes sensor data to the other components.
-
That sensor data is mirrored into a data lake that is provided by Red Hat Open Container Storage. Data scientists then use various tools from the open source project Open Data Hub to perform model development and training, pulling and analyzing content from the data lake into notebooks where they can apply ML frameworks.
-
Once the models have been tuned and are deemed ready for production, the artifacts are committed to git which kicks off an image build of the model using OpenShift Pipelines (Tekton).
-
The model image is pushed into the integrated registry of OpenShift running in the core data center which is pushed back down to the factory data center for use in inferencing.
In addition, Red Hat’s partner ecosystem is strategic to solving these use cases. The Seldon Core open source platform for deploying machine learning models is used in this solution to provide the cloud-native model wrapping, deployment, and serving.
Putting it all together
Building on top of the open source, highly customizable Kubernetes-based Red Hat OpenShift platform can prepare your technology stacks for the future. And when used in combination with the various elements of Red Hat’s software portfolio, you can benefit from a powerful foundation for building out a true AI/ML driven, edge-based manufacturing process, complete with sensors and the open hybrid cloud behind it all.
To learn more about Red Hat’s edge computing approach, visit our article on why Red Hat for edge computing.
저자 소개
Frank Zdarsky is Senior Principal Software Engineer in Red Hat’s Office of the CTO responsible for Edge Computing. He is also a member of Red Hat’s Edge Computing leadership team. Zdarsky’s team of seasoned engineers is developing advanced Edge Computing technologies, working closely with Red Hat’s business, engineering, and field teams as well as contributing to related open source community projects. He is serving on the Linux Foundation Edge’s technical advisory council and is a TSC member of the Akraino project.
Prior to this, Zdarsky was leading telco/NFV technology in the Office of the CTO and built a forward deployed engineering team working with Red Hat’s most strategic partners and customers on enabling OpenStack and Kubernetes for telco/NFV use cases. He has also been an active contributor to open source projects such as OpenStack, OpenAirInterface, ONAP, and Akraino.
Software, solution and cloud architect. Innovator, global collaborator, developer and machine learning engineer.
채널별 검색
오토메이션
기술, 팀, 인프라를 위한 IT 자동화 최신 동향
인공지능
고객이 어디서나 AI 워크로드를 실행할 수 있도록 지원하는 플랫폼 업데이트
오픈 하이브리드 클라우드
하이브리드 클라우드로 더욱 유연한 미래를 구축하는 방법을 알아보세요
보안
환경과 기술 전반에 걸쳐 리스크를 감소하는 방법에 대한 최신 정보
엣지 컴퓨팅
엣지에서의 운영을 단순화하는 플랫폼 업데이트
인프라
세계적으로 인정받은 기업용 Linux 플랫폼에 대한 최신 정보
애플리케이션
복잡한 애플리케이션에 대한 솔루션 더 보기
오리지널 쇼
엔터프라이즈 기술 분야의 제작자와 리더가 전하는 흥미로운 스토리
제품
- Red Hat Enterprise Linux
- Red Hat OpenShift Enterprise
- Red Hat Ansible Automation Platform
- 클라우드 서비스
- 모든 제품 보기
툴
체험, 구매 & 영업
커뮤니케이션
Red Hat 소개
Red Hat은 Linux, 클라우드, 컨테이너, 쿠버네티스 등을 포함한 글로벌 엔터프라이즈 오픈소스 솔루션 공급업체입니다. Red Hat은 코어 데이터센터에서 네트워크 엣지에 이르기까지 다양한 플랫폼과 환경에서 기업의 업무 편의성을 높여 주는 강화된 기능의 솔루션을 제공합니다.